Concept of Industry 5.0
Industry 5.0, symbolizing the fifth industrial revolution, is based on collaboration between humans and advanced technologies such as artificial intelligence, robotics, 3D printing, and the Internet of Things (IoT). The goal of this model is to achieve greater efficiency and flexibility in production processes while promoting sustainable development that considers ecological and social aspects. In Industry 5.0, technologies work alongside employees instead of replacing them, creating a more humane production model beneficial for both businesses and society.
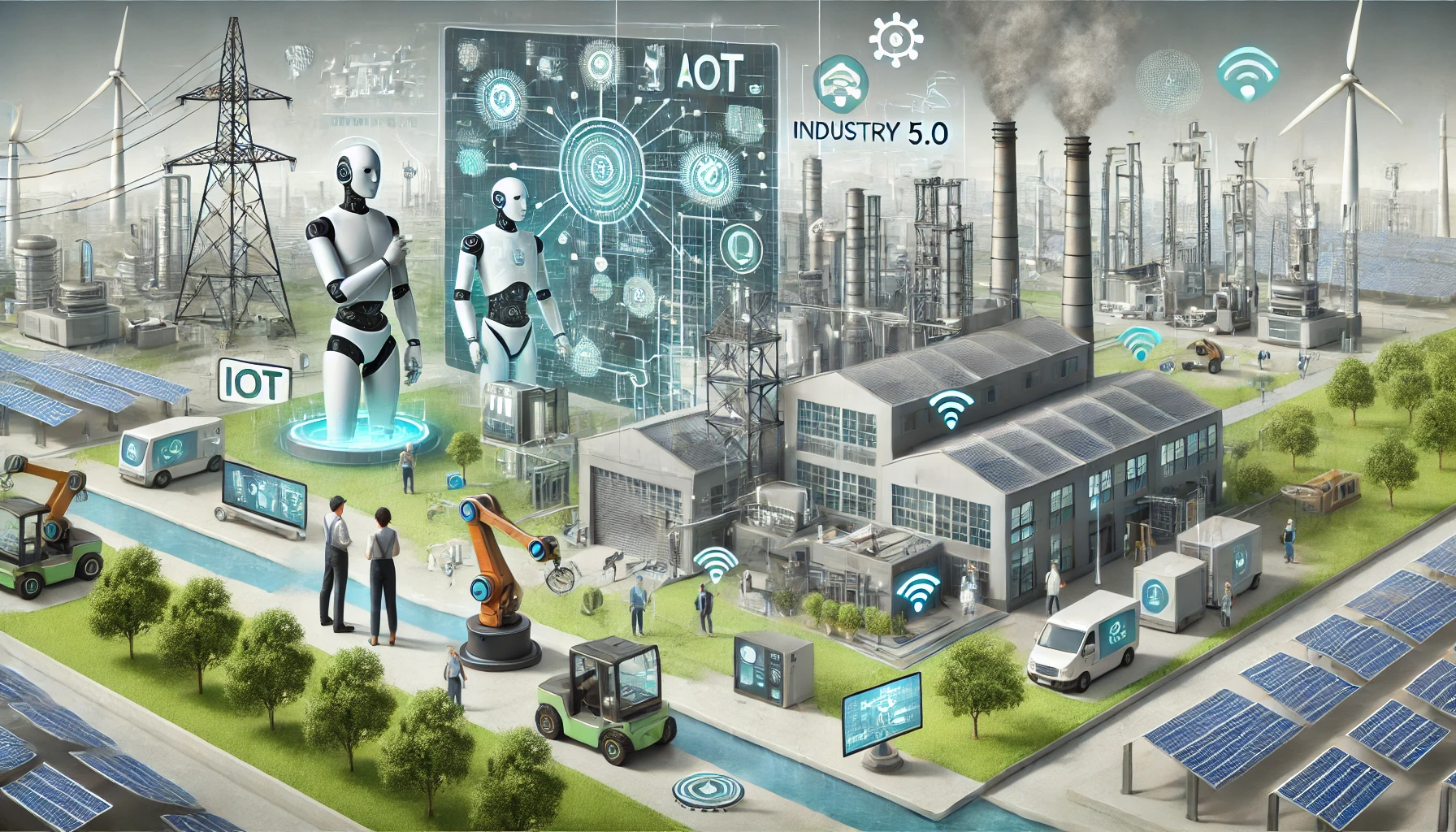
The principles of Industry 5.0 also include promoting collaboration between businesses, scientific institutions, and governments to jointly create innovative solutions for the future. This transformation also assumes a greater role for humans in production processes, rather than seeking to replace them with machines, emphasizing the human dimension and value in modern production systems.
Key Elements of Industry 5.0
- Human factor: The fifth industrial revolution will introduce greater use of cobots, or collaborative robots, which will work alongside humans throughout the production process. Cobots, easier to program and ideal for performing repetitive, hazardous tasks, will allow people to focus on more complex operations requiring cognitive abilities. This will result in new roles, requirements, and training and educational needs.
- Process Management in Plants (PPM): Industry 4.0 introduced digitization and artificial intelligence to PPM, while Industry 5.0 will focus on collaboration. Digitization enables the collection of vast amounts of data, and artificial intelligence allows for data analysis and scenario creation. In Industry 5.0, people will use their knowledge and intuition to make final decisions, maintaining full responsibility for the operation of the plant.
- Mass Customization: Consumer expectations will change, and product customization will become crucial. Industry 4.0 focused on cost reduction with some emphasis on customization, while Industry 5.0 will prioritize customization thanks to advanced technologies enabling on-demand production.
- Sustainable Development: Industry 5.0 will place a strong emphasis on renewable energy sources. Manufacturers will strive to create energy-efficient processes that reduce their carbon footprint.
Development of Industry 5.0 Technologies
Smart production systems 5.0 are advanced technologies that optimize production processes through data analysis, machine learning, and automation. Thanks to them, the production process in Industry 5.0 becomes more efficient, flexible, and sustainable. Smart production systems 5.0 ensure better product quality control and reduction of raw material waste, leading to greater market competitiveness and increased company profits.
Technologies in Industry 5.0
Technologies in Industry 5.0 are advanced solutions aimed at increasing efficiency, flexibility, and sustainable development of production processes. The most important of these include:
AI enables real-time data analysis, failure prediction, and process optimization. Thanks to learning algorithms, systems can automatically adapt to changing conditions, improving efficiency and precision.
Cobots are robots designed for safe collaboration with humans. Using advanced sensors and algorithms, they can perform precise, repetitive tasks while increasing safety and comfort for human operators.
IoT includes a network of connected devices that monitor and manage production by collecting and analyzing data. This allows for remote monitoring and optimization of operations, increasing efficiency and reducing downtime.
3D printing allows for rapid prototyping and on-demand production of customized parts. This technology enables the creation of complex geometries that would be difficult to achieve with traditional methods, contributing to innovation and production flexibility.
Machine learning is a branch of AI that allows systems to learn from data, identifying patterns and optimizing processes. In production, it can be used to predict machine failures, optimize logistics, and adjust production processes to changing conditions.
Big Data analysis involves processing large data sets from various sources to gain valuable insights. In industry, this allows for trend prediction, production optimization, and better resource management.
Cloud computing offers access to powerful computing resources and data storage from anywhere. This enables more flexible production management, rapid resource scaling, and easy collaboration between different locations.
Blockchain ensures transparency and security in the supply chain, enabling the tracking of every stage of production and logistics. This reduces the risk of counterfeiting and increases trust between business partners.
Benefits of Production Process Automation 5.0
Industrial automation 5.0 involves the integration of advanced technologies such as robotics, artificial intelligence, and the Internet of Things (IoT) to optimize production processes. It brings many benefits, including:
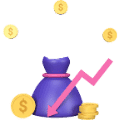
Cost Reduction in Production:
Automation allows for the reduction of operational costs by increasing efficiency and minimizing waste.
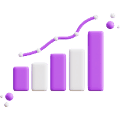
Increased Efficiency:
Automation makes it possible to speed up production processes, leading to higher productivity.
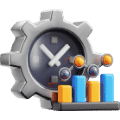
Improved Product Quality:
Advanced monitoring and quality control systems help maintain high production standards.
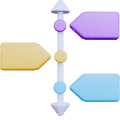
Reduced Risk of Errors:
Automation minimizes the risk of human errors, resulting in less waste and higher final product quality.
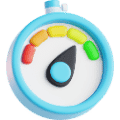
Better Resource Utilization:
Smart resource management systems enable more efficient utilization, increasing production profitability.
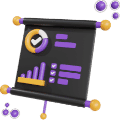
Increased Competitiveness of Enterprises:
Companies implementing modern technologies gain a competitive edge through innovation and production flexibility.
It is worth noting that the automation of production processes 5.0 does not eliminate the role of humans but supports the collaboration between employees and modern technologies. This synergy allows for better results than traditional production methods.